Maneje piezas complejas
Adquiera la capacidad para realizar el desbaste y el acabado en un solo proceso mediante las herramientas NBZ215 y MZN410R de Niagara Cutter para aplicaciones de fresado en duro. En lugar de los métodos tradicionales que requieren múltiples configuraciones, que en algunos casos incluyen el maquinado por descarga eléctrica (EDM), la opción para fresado en duro permite reducir los plazos de entrega y aumentar la productividad gracias a que elimina las configuraciones múltiples y los complejos procesos de pulido.
Con el aumento en el área de la fabricación de moldes y matrices en el mercado, existe una creciente necesidad por contar con una completa gama de métricas para los productos MBZ215 y MZN410R/510R de Niagara Cutter. Por esta razón, se amplio la gama para incluir cortadores de metal con puntas esféricas desde 0,5 mm hasta 12 mm de diámetro y cortadores de metal de alto avance desde 2 mm hasta 12 mm de diámetro.
Estas familias de herramientas son eficaces en aceros endurecidos de 48-65 HRc, super aleaciones de hierro fundido y con base de níquel. Con estas recientes incorporaciones, la versatilidad de la familia de herramientas ha alcanzado nuevas dimensiones en el área del fresado exigente de alta velocidad.
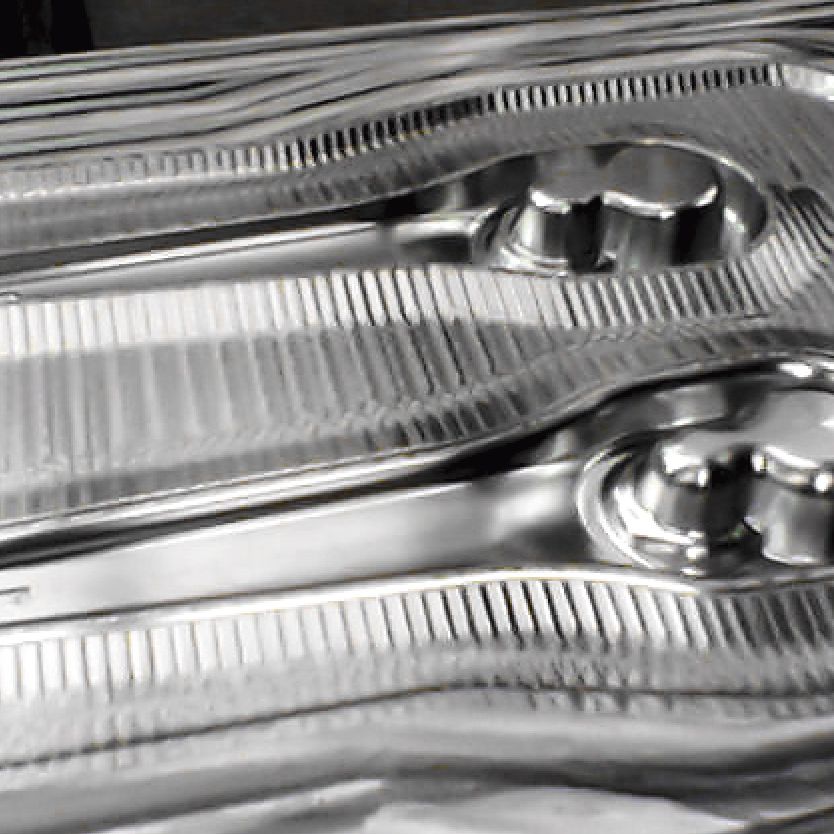
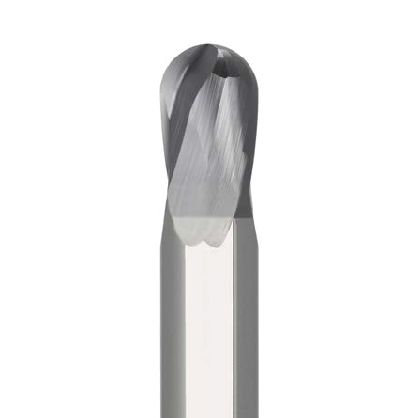
MB215, MBZ215, MZ645 Y MZ645R
FRESADO EN DURO DE ALTA VELOCIDAD
Las herramientas de serie MBZ215 fueron diseñadas al servicio del fresado en duro de moldes y matrices. Están fabricados para lograr el máximo rendimiento en aleaciones y herramientas de acero de 48 HRc a 65 HRc. Proporcionan un mejor rendimiento cuando se utilizan en procedimientos de desbaste o acabado de copiado.
Estos cortadores de metal se producen a partir de un avanzado sustrato de carburo de micro grano y se proporcionan con un recubrimiento AlTiN resistente a las altas temperaturas y la abrasión.
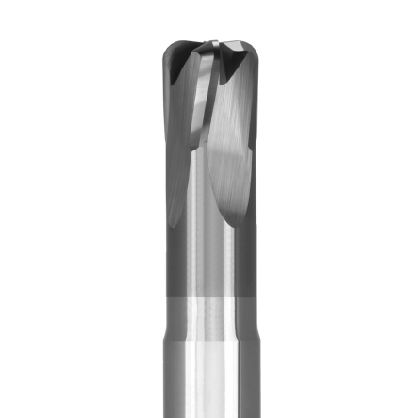
MZN410R Y MZN510R
FRESADO EN DURO DE ALTO AVANCE
Las series MZN410R y MZN510R están diseñadas para maximizar la productividad en aceros endurecidos y superaleaciones.
Estos cortadores tipo endmill poseen un un sustrato optimizado, geometría y recubrimiento que garantizan la confiabilidad del proceso.
Estos cortadores de metal de AlTiN recubiertos son eficaces en aceros endurecidos, fundidos y super aleaciones con base de níquel. Una aplicación típica para este cortador cuando se realizan operaciones de mecanizado en materiales de acero templados utilizados en moldes y matrices.
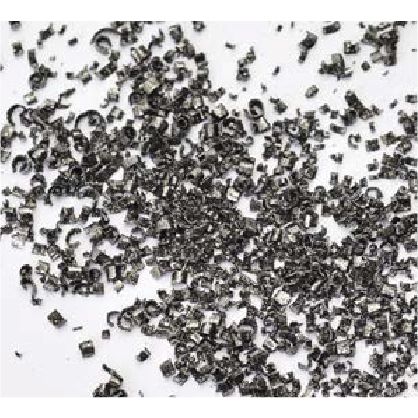
Evite el recorte de virutas de una vez por todas
El diseño de diente de extremo abierto del modelo MZN410R/510R proporciona una excelente eliminación de virutas. La fiabilidad del proceso se logra porque las virutas se eliminan efectivamente de la zona de corte y no vuelven a cortarse, lo que evita el despostillamiento del filo de corte.
CONSEJOS DE FRESADO EN DURO Estrategia altamente eficaz para operaciones de mecanizado complejas
1. MANTENGA UNA VELOCIDAD DE AVANCE Y CARGA CONSTANTE
Uno de los conceptos que más se pasa por alto cuando se trata de fresado es el de mantener una velocidad de avance y carga constantes. Las superficies complejas y las trayectorias de corte utilizadas en la industria de moldes y matrices ocasionan que las máquinas herramienta presenten una rápida fluctuación en la velocidad de avance, lo que genera una considerable pérdida de la vida útil de la herramienta. La velocidad de avance siempre presentará fluctuaciones, a menos que la máquina se utilice en línea recta.
Cuando se trabaja en superficies exigentes, se debe considerar que las máquinas herramientas no reducen las rpm en conjunto con reducciones de la velocidad de avance. Una buena regla general es que si la velocidad de avance programada no puede mantenerse un 80 % del tiempo, la velocidad de avance promedio debe reducirse. Entonces, la velocidad de avance y la rpm deben reducirse en el programa; por ejemplo, las rpm programadas son de 30 000 y la velocidad de avance es de 150 ipm. Sin embargo, la velocidad de avance que se mantiene en promedio es solo de 75 ipm; por consiguiente, las rpm deben reducirse a 15 000. Esta reducción de las rpm puede aumentar la vida útil de la herramienta hasta en un 50 %, además de tener un impacto poco significativo en el tiempo de ciclo.
2. NO DEJE MUCHO MATERIAL EN EXCESO PARA EL ACABADO
Cuando se realizan operaciones de mecanizado en materiales de acero por sobre los 48 HRc, dejar demasiado material para el acabado no solo reducirá la producción sino que también puede causar estragos en el acabado de la superficie y la vida útil de la herramienta. Una guía general para el sobrematerial de superficies para el acabado es dejar entre un 1 % y 2 % del diámetro del corte de acabado.
La mayoría de los fabricantes de herramientas de corte basan sus datos de corte de acabado en un 1 % a 2 % del diámetro de acoplamiento de la herramienta. Dejar más material que esto ocasionará una pérdida en la productividad. Por ejemplo; cuando se utiliza un diámetro de 1/2" de la herramienta, es mejor no dejar más de 0,005" a 0,010" de sobrematerial.
3. DEJE UN SOBREMATERIAL CONSISTENTE EN TODAS LAS SUPERFICIES PARA CONSEGUIR LA MÁXIMA VIDA ÚTIL DE LA HERRAMIENTA
Dejar demasiado material para el acabado es malo para la vida útil de la herramienta y los acabados de las superficies. Dejar un sobrematerial no consistente para el acabado tampoco es lo óptimo, si no que peor. Después del desbaste de superficies complejas, es importante que la herramienta realice una trayectoria de descanso del desbaste o de semi acabado, con el fin de garantizar un sobrematerial para el acabado que sea consistente en todas las superficies. Considere el siguiente ejemplo: se realizó el fresado en desbaste de una superficie compleja en 3D con un cortador de punta esférica de 12 mm con un diámetro de corte de acabado previsto de 8 mm.
Una práctica segura sería realizar una trayectoria de desbaste de descanso con un cortador de punta esférica de 10 mm. Luego,una trayectoria de semi acabado con un cortador de punta esférica de 8 mm, asegurándose de que solo haya un sobrematerial de entre 0,003" y 0,006" en todas las superficies. Por último, finalizar el proceso de fresado con un cortador de punta esférica de 8 mm para lograr un acabado consistente en la superficie y extender la vida útil de la herramienta de acabado. Esta estrategia incluso permite utilizar el cortador de punta esférica como una herramienta de semi acabado una vez que finalice la vida útil de la herramienta.
4. NO TODOS LOS ACEROS ENDURECIDOS TIENEN LA MISMA FABRICACIÓN
Algunos aceros endurecidos comunes en la industria de moldes y matrices presentan desafíos únicos. Consideremos, por ejemplo, el acero D2, que puede tratarse a 60-62 HRc. Debido al contenido de cromo agregado, este tipo de acero no solo es duro, sino que también complejo. Además, el mecanizado es similar a aceros de entre 62 y 65 HRc.
El acero inoxidable 420 también es muy común en la industria de moldes, debido a que es resistente al desgaste y puede pulirse con acabado espejo. A pesar de que este material se trata típicamente con calor a 48-52 HRc, sigue conservando sus propiedades de acero inoxidable pegajoso. Este material es propenso a causar recrecimiento de filo (BUE), por lo que utilizar la velocidad de avance por minuto apropiada es fundamental. Utilizar mezcla de aceite pulverizado o aire también contribuirá a reducir el BUE durante el mecanizado de este material.
5. UTILICE SOPORTES RÍGIDOS
Para conseguir la máxima vida útil de la herramienta, los soportes de alta precisión son fundamentales para el fresado en duro.
El run-out debe mantenerse a menos de 0,0004". Este tipo de precisión puede lograrse con la mayoría de los portaherramientas de ajuste por contracción térmica, soportes de fresado, porta pinzas de alta precisión y soportes de cortadores de fabricantes seleccionados. Un portaherramientas de precisión garantiza la exactitud del proceso, mientras que un portaherramientas menos seguro ocasionará que la vida útil de la herramienta sea impredecible y generará la intolerancia a ciertas superficies.
6. SIGA LOS PARÁMETROS DE CORTE RECOMENDADOS
Después una meticulosa investigación y años de experiencia práctica, hemos desarrollado parámetros recomendados específicos de corte. Estos datos de corte están optimizados según el diseño, especificaciones y grupos de material de la herramienta.
Siempre deben utilizarse como punto de partida y luego pueden realizarse modificaciones en función de la aplicación.